7 Essential Components of Sample Shipping Policies That Reduce RFP Processing Time
7 Essential Components of Sample Shipping Policies That Reduce RFP Processing Time - Standard vs Express Shipping Cost Structure For International Orders
For international orders, understanding the difference in pricing between standard and express shipping is crucial. Standard shipping is generally the cheaper option, best suited for items that don't have a tight deadline. Express shipping, on the other hand, emphasizes speed, usually delivering within a day, but at a higher cost. This price difference is tied to factors like the value of the item, the company's budget, and how important fast delivery is to the customer. In some cases, express services may include extra insurance and care for fragile or high-value goods, offering an added layer of protection. In the end, the decision of whether to use standard or express shipping depends on customer expectations and the overall business strategy. Businesses must find a balance between how fast items need to be delivered and the costs associated with different shipping methods.
When examining international shipping costs, it's clear that standard and express options have unique cost structures. Factors like weight, size, and distance are foundational, but the picture becomes more complex with the addition of customs, handling, and fuel surcharges. Express options, due to their expedited nature, tend to carry higher surcharges, something to consider when planning for international logistics.
While express shipping promises rapid delivery, relying on these timelines can be precarious. Flight availability and customs hurdles can significantly impact express delivery times, potentially causing delays and cost overruns, especially when urgency is paramount. In contrast, standard shipping often offers a more predictable delivery window, even if it takes longer.
The specific cost structure can also vary dramatically between carriers. Some carriers might specialize in certain geographic regions or types of goods, leading to variations in pricing. Thorough research on various carriers and their individual cost models is essential for finding the best fit for a particular international shipping scenario.
Holiday seasons or any periods of peak shipping activity can exacerbate cost differences. Express options are especially sensitive to these changes as the demand surge coupled with limited capacity often drives up prices. This price sensitivity should be factored into any budget forecasts that depend on international shipping.
Something that influences the cost of shipping, for both standard and express options, is the concept of dimensional weight. This factor often means that package size matters more than its actual weight. A lightweight but large package might end up being more costly to ship than a heavier, more compact one. Understanding the weight-size relationship is key for optimizing shipping costs.
Customs regulations present another layer of complexity, especially for express shipping. Even though express options are often prioritized for faster processing, the variability of customs procedures in different countries and the unique requirements of certain types of goods can influence the overall cost. It's not always clear-cut that 'faster' means 'cheaper'.
Interestingly, the availability of shipping insurance might be less expensive and more beneficial with standard shipping. While the inherent risk of damage might appear higher for express due to faster transit and multiple handling, a thorough evaluation of risk vs cost is necessary when choosing between options, particularly for valuable items.
Companies that ship frequently may benefit from volume discounts, but this aspect can be more challenging with express shipping. The premium pricing structure that underpins express options makes it harder to negotiate substantial savings, highlighting the importance of building and nurturing long-term relationships with carriers for optimal cost benefits.
When a shipment needs to be returned, the cost structure for standard and express can differ significantly. Express services often charge more for returns, potentially eroding the initial savings that a business might have realized. It is essential to consider the potential for returns during the shipping policy design.
The terms and conditions of payment also present differences. While standard shipping options sometimes provide flexibility like net payments on larger shipments, express shipments often require upfront payment, which can affect a business’s cash flow. Businesses dependent on rapid international deliveries for operations will need to account for this in their financial planning.
In conclusion, understanding the intricacies of both standard and express shipping options is vital. The interplay of a diverse set of factors influences shipping costs, and awareness of those factors is key for streamlining logistics and maintaining profitability.
7 Essential Components of Sample Shipping Policies That Reduce RFP Processing Time - Automated Tracking Number Assignment Within 4 Hours of Purchase
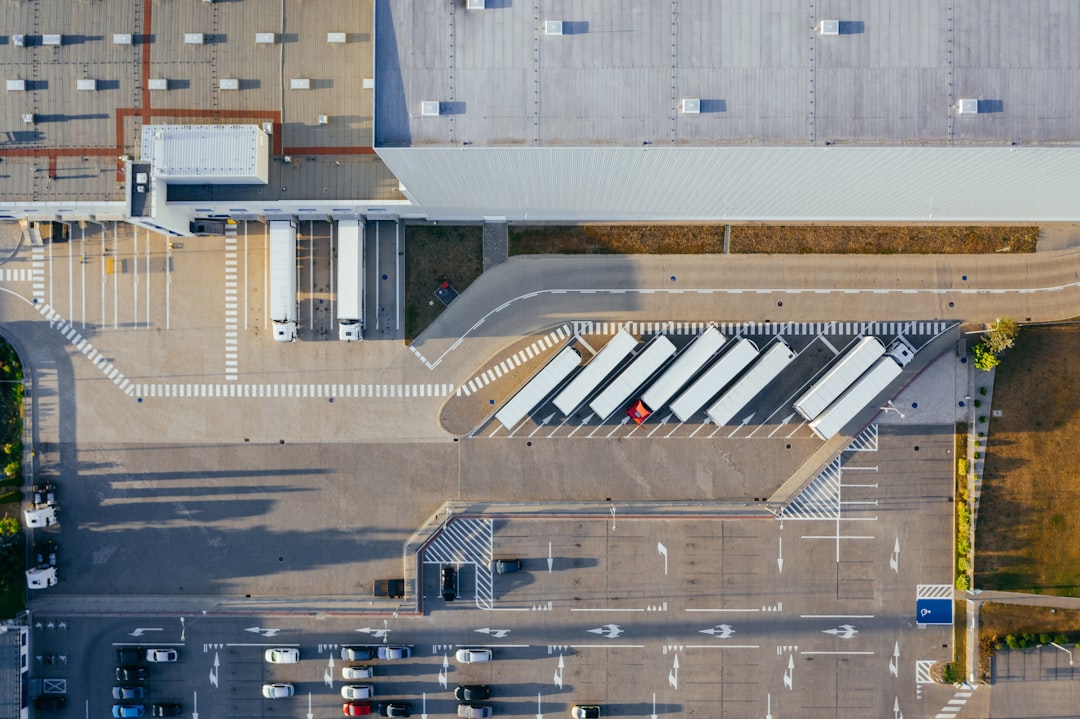
Automating the process of assigning tracking numbers within four hours of a purchase significantly improves shipping efficiency. By automatically generating these numbers, businesses can instantly give customers access to their order's status, building trust and transparency. This automation eliminates potential human errors from manual data entry and smooths out communication about order fulfillment. Furthermore, prompt tracking information reduces customer anxieties and elevates the overall customer experience. In the ever-changing world of online shopping, incorporating automated systems like this is becoming crucial for businesses looking to fine-tune their shipping policies and increase customer happiness. While fast order fulfillment is a major factor in the shopping experience, it's notable that the "within four hours" constraint could be difficult to manage in certain businesses and shipping situations, but the general concept of faster turnaround is still a strong competitive advantage.
Within the realm of e-commerce fulfillment, the ability to automatically assign a tracking number within a mere four hours of a purchase is a noteworthy development. This swift action provides near-instantaneous updates to both the seller and buyer, dramatically increasing the transparency of the shipping process. It's like a live window into the shipment's journey, fostering trust and open communication.
This automation is powered by intricate algorithms that interface with various logistics software. It streamlines tracking and significantly reduces human errors, which are a common pitfall of manual assignment methods. It's like having a digital assistant meticulously managing the tracking numbers, making the process less susceptible to slips and mistakes.
There's a clear connection between automated updates and customer loyalty. Research suggests customers who receive timely tracking updates are more likely to return, suggesting this automated feature is key in fostering customer retention. It makes sense, as customers seem to appreciate the transparency and reassurance that tracking provides.
The implementation of automated tracking number systems has the added benefit of freeing up human resources. These systems can tackle a substantial portion of the administrative workload involved in logistics, which can represent a significant chunk of overall processing time. By taking over this burden, valuable employee time can be redirected to higher-priority tasks. However, it's worth investigating if this automation also contributes to a potential reduction in the workforce.
Some automated systems are also capable of assigning tracking numbers based on pre-set rules like the chosen shipping method or package dimensions. This functionality empowers companies to instantly optimize their shipping approaches, allowing them to better adapt to changing demand. But one might question how these criteria are chosen and whether it truly optimizes shipping costs compared to other methods.
For businesses operating in the competitive e-commerce landscape, faster shipping can be a major differentiator. Automating the tracking number assignment can shorten the average time to ship by a significant margin, which can be a powerful way to outpace rivals and attract customer attention. It's a classic example of how technological efficiencies can translate into a competitive edge.
When an automated tracking system integrates with inventory management software, real-time stock levels become instantly accessible. This real-time integration effectively prevents overselling situations. It ensures that only items currently available are sold, which improves operational efficiency and reduces the frustration associated with canceled orders. Although, if real-time data is available, is it necessary to maintain separate inventory management systems? Can this be automated away too?
Manual methods of tracking numbers are prone to errors, leading to misplaced shipments. Automated systems can significantly reduce these errors, boasting accuracy rates well above those of manual processes. However, the claim of over 95% accuracy in automated systems should be examined for potential biases in the data collected. Is it comparing apples to apples?
The wealth of data produced by automated tracking can be incredibly valuable for business analysis. Companies can analyze shipping patterns and customer behavior, leading to improvements in forecasting and planning. However, companies need to be careful not to use this data for nefarious purposes.
Finally, the capacity to quickly issue a tracking number within just four hours positively impacts customer satisfaction. In especially busy shopping periods, the speed and reliability of this automated system can become a critical competitive advantage. However, the actual impact on customer satisfaction and customer service may also be tied to factors outside of merely delivering tracking numbers. There might be other more important factors to consider when evaluating the value of faster delivery and tracking numbers.
7 Essential Components of Sample Shipping Policies That Reduce RFP Processing Time - Temperature Control Requirements For Perishable Items During Transit
Ensuring perishable items like food and medicines remain safe and usable during transportation requires strict temperature control. Maintaining the right temperature range is essential for preserving quality and safety, with deviations posing risks of spoilage or even health hazards. This is particularly important in the cold chain, where a complex system of temperature-controlled processes safeguards perishable goods. To support this, strong regulations and standards are in place to ensure proper handling and storage throughout the entire transit process, minimizing risks.
These requirements necessitate sophisticated strategies that avoid temperature fluctuations during shipping. This means using specialized containers and real-time monitoring technologies. Such advanced methods ensure products remain within specific temperature ranges from origin to destination, especially crucial for certain products.
The landscape for temperature control is not static. There are expected shifts in regulation for certain products in 2025, likely impacting both food and pharmaceuticals. Shippers will need to keep abreast of these changes to maintain compliance and manage the potential consequences of non-compliance. Ultimately, consistently applying proper temperature control during shipping builds customer trust, helps meet regulatory standards, and strengthens a business's reputation for product quality and safety.
Maintaining the right temperature during the journey of perishable goods is crucial for keeping them safe and in good condition. This is especially important because bacteria grows much faster in a temperature range we call the "Danger Zone," roughly between 40°F and 140°F. It's critical to avoid this range during transport to prevent spoilage and potential health risks.
Proper temperature control can really extend the shelf life of perishable products. For example, keeping milk or yogurt consistently below 35°F can potentially double its freshness. This is because low temperatures slow down the rate of chemical reactions that cause spoilage. However, we must understand that this doesn't mean every product is exactly the same.
Innovations in packaging are changing how we ship sensitive items. Things like phase-change materials can keep things at a steady temperature for a long time without needing electricity, opening up possibilities for shipping perishables over much longer distances. It's intriguing to think about how these new materials might further impact shipping.
It's not always simply a matter of cold. Some products, like raw meat, require not only refrigeration but also very specific humidity levels. Too much moisture can cause it to spoil, so we need specialized containers to manage both temperature and humidity for these types of products. It's a subtle but important factor to consider.
Each product has a different ideal temperature. For example, fresh vegetables tend to stay freshest around 33°F, while frozen food, obviously, needs to be at or below 0°F to avoid thawing. It's important to know the precise temperature needs of the products being shipped and to design transport accordingly.
New technologies like RFID tags allow for real-time tracking of temperature during transit. We can get instant alerts if the temperature goes outside the set range. These alerts are important, especially for long or complex journeys, as they can prevent massive losses due to spoiled goods. However, it would be valuable to evaluate the accuracy and reliability of these sensors in various environmental conditions.
Research suggests that a product's quality can degrade by as much as 25% when exposed to big temperature swings. This points to the importance of really consistent and precise temperature management, especially for sensitive items like some medications or seafood. There's a direct connection between temperature control and quality.
Moving perishable goods might involve a variety of transport methods. We can use refrigerated trucks, climate-controlled shipping containers on ships or planes, and each stage of the journey has to meet specific temperature standards. It is critical that all links in this cold chain are consistent and compliant to guarantee the quality of the product. How these varied requirements are standardized and regulated across different sectors and locations is an important open question.
Rules and regulations, often set by agencies like the FDA, dictate specific temperature requirements for many food items, especially those easily contaminated like seafood and poultry. There can be serious legal consequences, potentially harming the profitability of a business, if these regulations aren't followed. Understanding the exact regulatory requirements for each type of product in the intended regions of delivery is an important part of ensuring compliance.
Good temperature control procedures protect the products and also increase consumer trust. Studies suggest that people are more inclined to buy from companies that are known for keeping their products at the right temperature during transport. It appears that good temperature control is not only a technical or compliance issue but also plays a role in branding and consumer relations. However, the nature of this connection is still an area for deeper research, especially as it relates to a variety of consumer preferences and sensitivities.
7 Essential Components of Sample Shipping Policies That Reduce RFP Processing Time - Package Weight Restrictions And Multi Box Handling Guidelines
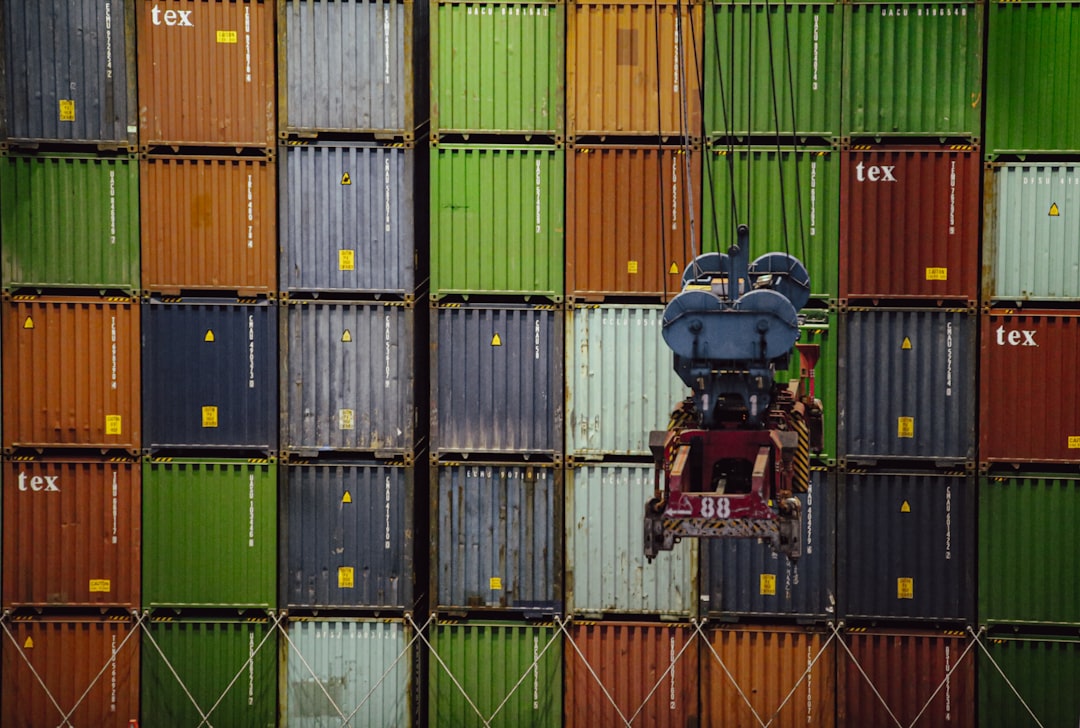
Defining clear package weight restrictions and multi-box handling procedures within your shipping policies is crucial for smooth and efficient order fulfillment, which can significantly impact RFP processing times. These guidelines help manage both the physical constraints of shipping and the associated costs.
For example, understanding the maximum weight a box can safely hold is essential to prevent damage or breakage during transit. It's not just about the weight listed on a box – manufacturers often include a box strength certificate indicating its capacity. This knowledge helps in choosing the right type of box for the job, and potentially preventing costly replacements and reshipments.
Beyond individual package limits, handling shipments containing multiple boxes requires a careful approach to ensure accuracy and prevent confusion. Businesses should clearly outline how to calculate total billable weight for such shipments, especially since shipping costs are often tied to either actual or dimensional weight (whichever is greater). Neglecting to consider this can lead to unforeseen charges or billing discrepancies.
Protecting goods during shipping isn't optional. Including instructions on using adequate cushioning materials and encouraging the use of sturdy packaging, like double-walled boxes for heavier items, or even nesting smaller boxes within larger ones, minimizes damage risks.
While these guidelines might appear basic, they are foundational to optimizing your shipping processes. Failing to account for weight limits or adhering to proper handling practices for multiple boxes can increase processing times as issues are discovered later in the shipping cycle. By incorporating these elements into your policies, businesses can improve clarity for customers and reduce processing delays that hinder timely order delivery.
The aim is to present clear, transparent, and predictable shipping processes that make the entire experience as smooth as possible for everyone.
When it comes to shipping packages, especially multiple ones as part of a single order, understanding weight restrictions and how carriers handle these shipments is vital. Carriers often base their pricing on a package's size as much as its actual weight. This means a large, lightweight box can cost more to ship than a smaller, heavier one. It's a curious interplay of volume and mass that can impact shipping costs.
If you're shipping multiple boxes, the total weight of all those boxes must usually stay under the carrier's maximum allowed weight. But things get more intricate if the boxes have vastly different weights. Keeping track of the overall weight becomes crucial to avoid extra charges or unexpected rerouting of the shipment.
Shipping companies typically offer guidelines on the best ways to pack multiple boxes within a single order to ensure they stay secure and arrive in good condition. Improper packing can lead to higher shipping costs and even damage to the items being transported. A haphazard approach is clearly not optimal.
Carriers often have specific instructions on how to handle multi-box shipments. For instance, labeling each box as part of a set is common. Ignoring these instructions can create confusion and increase the chance of a box being damaged or misplaced during transit. It makes you wonder if carriers could do a better job of standardizing these instructions and offering clear and easy-to-understand guides.
There are specific rules on how weight should be balanced across boxes within a multi-box shipment. This is to make sure the packages don't shift during transport, potentially causing damage. It's a bit like balancing a complex puzzle with the goal of achieving stability throughout the shipping journey.
The type of packaging material you use can add to a package's overall weight and therefore the shipping cost. Using heavy-duty packaging might seem like a good idea to protect your items but could make the shipment considerably more expensive. Examining different packaging choices and balancing protection with weight seems like an engineering puzzle that could lead to significant cost optimization in many circumstances.
The labeling of each box in a multi-box shipment is essential for clear identification and proper handling. Correct labeling allows the carrier to treat each package according to its weight category. Incorrect labeling can cause the carrier to deviate from the planned handling, which can cause all sorts of unforeseen complications. A clear and standardized labeling system for packages seems like a possible area for research to help minimize errors in the logistics chain.
Certain items may have their own specific weight restrictions, especially when included in multi-box shipments. These limits are often set by the carrier, so understanding them is critical to avoid unexpected shipment delays or extra fees. These idiosyncrasies across shipping carriers and different item types do present interesting research opportunities into potential areas of standardization.
Insuring multiple packages can get complex if the boxes have varying values. This impacts the overall cost of insurance for the entire shipment. It would be interesting to research if there are more optimized insurance pricing models to minimize unnecessary complexity.
Each carrier has its unique weight and handling procedures for multi-box shipments. These can significantly impact the cost and speed of the shipment. The lack of uniformity across carriers suggests that a comparative study of carrier services from a cost-benefit perspective would be useful for shippers to select optimal services based on their requirements. It's interesting to think about how shipping could be standardized and optimized if this information was easier to obtain and understand.
In conclusion, managing multiple packages involves intricate considerations regarding weight, packaging, and compliance with carrier policies. Understanding these nuances allows shippers to optimize their shipping strategies for both cost and efficiency. This suggests that a comprehensive database of carrier restrictions and handling practices would be incredibly valuable, especially for businesses dealing with complex international logistics.
7 Essential Components of Sample Shipping Policies That Reduce RFP Processing Time - Return Address Labels And Documentation Requirements
Having clearly defined return address labels and required documentation is essential for smoothly handling returns, which directly impacts how quickly an RFP is processed. Well-designed return labels, easy to read and in the correct format, can prevent delays in getting refunds or exchanges. It's vital to be upfront about who covers return shipping costs and the specific situations where returns are permitted. When shipping internationally, adhering to customs regulations and completing the necessary paperwork is crucial to avoid any problems. Including easy-to-find return address information in shipping policies can enhance customer satisfaction and contribute to the entire transaction being more efficient. However, one might question the necessity of certain documents and whether they genuinely enhance customer service or introduce complexity. It might be possible to achieve similar goals with simplified procedures.
Return address labels, while seemingly simple, play a crucial role in efficient logistics, especially when dealing with returns. Using pre-printed labels streamlines the process, reducing the time spent on manually addressing packages. However, poorly formatted or unclear labels can easily lead to packages being sent to the wrong location, emphasizing the importance of accuracy. This precision becomes even more critical when navigating international shipments, where adherence to customs regulations is vital.
Shipping policies should always require specific forms and documentation during the return process. Missing information leads to unnecessary delays, potentially causing frustrations for customers and impacting business operations. The complexity increases when goods are shipped across international borders where customs officials closely scrutinize documentation. Inaccurate or missing details on return labels can result in substantial penalties and even confiscation of goods, which highlights the serious repercussions of non-compliance.
Digital return labels are gaining prominence, offering advantages in efficiency. Businesses can easily reprint labels when needed, quickly adapting to changes in the return process. This agility contributes to a smoother customer experience. But there's a caveat: shipping carriers often have varying requirements for return labels. Businesses must understand these nuances to avoid confusion during returns, particularly for international shipments where these complexities are amplified.
When discussing returns, the costs associated with shipping cannot be ignored. The costs associated with return shipping can vary substantially based on the carrier used and the destination. Businesses must carefully consider these variables when constructing their shipping policies to ensure they don't incur unnecessary expenses. Understanding the interplay between these cost factors and choosing the most appropriate carrier for the return shipment is important.
Furthermore, the integration of automated systems for printing return labels reduces the risk of human error, a frequent issue in manual processes. This automation can significantly improve accuracy, which directly translates to fewer errors in shipping labels and subsequently, fewer misdeliveries. Returns are processed with greater speed and precision when automated systems are used, thus improving the overall return efficiency.
It is important to consider physical and dimensional weight when dealing with returns. Failure to address this factor on the return labels can create unexpected costs or complications, impacting both the business and the customer. It’s interesting that the same considerations that apply to initial shipments also apply to the return shipments, as though the journey of goods is somehow a mirrored reflection.
The realm of international returns is constantly evolving with ever-changing regulations. This dynamic environment necessitates businesses remain informed about evolving rules. Failing to stay updated on the current international regulations can result in severe consequences and disruptions in the return process. Staying informed is not just prudent, but vital for compliant international operations.
The use of return address labels and adhering to documentation requirements seems like a relatively simple concept, yet it is a critical element in smooth and efficient shipping operations, particularly for returns. It's an intriguing example of how seemingly minor details can impact complex systems and have consequences that range from minor inconveniences to major logistical problems.
7 Essential Components of Sample Shipping Policies That Reduce RFP Processing Time - International Customs Declaration Process And Documentation
International customs declarations and the accompanying documentation are critical for smooth international shipping. This process involves providing customs officials with detailed information about the goods being shipped. Key elements include the commercial invoice, which outlines the products and their value, and the export declaration, which details the specifics of what's being shipped, such as quantity and destination. The customs declaration itself acts like a passport for the goods, offering crucial information about the shipment's nature and value.
Accuracy is paramount in customs declarations to avoid delays and penalties during the clearance process. This underscores the importance of utilizing standardized forms and guidelines offered by shipping carriers and customs authorities. International shipping regulations are complex and often vary between countries, which makes correct and complete documentation even more important. By meticulously handling customs declarations and associated paperwork, businesses can help streamline their international shipping processes and improve overall efficiency. While this might seem like a relatively simple aspect of shipping, it's important to note that mistakes or oversights in this area can lead to significant delays and complications.
The international customs declaration process involves a complex web of regulations that vary greatly across nations. Each country establishes its own set of rules and required documentation, making it crucial for shippers to familiarize themselves with both their origin and destination country's requirements to avoid delays and penalties. This is further complicated by the use of Harmonized System (HS) codes, which are a global classification system for traded goods. Getting these codes wrong can lead to customs rejections or significant fines, highlighting the need for meticulous attention to detail in documentation.
The value of goods, used for calculating import duties and taxes, is determined using different valuation methods. Methods like transaction value, computed value, and deductive value can affect the final cost of shipping, and understanding which method is applied in each country is vital for budgeting and planning. It seems a bit odd that so many methods exist when it comes to assessing value, but it shows how the international logistics landscape is quite varied.
Fortunately, certain goods, particularly those below a specific value, are exempt from duties or taxes. This "de minimis" threshold varies from country to country, with examples like the US having a threshold of $800 while the EU has different rules. These exceptions are helpful for businesses seeking to reduce costs, but shippers have to keep track of these constantly changing regulations.
For larger shipments, bonded warehouses can be used to delay the payment of duties until the goods are removed. While it seems like a useful tactic to manage cash flow, it comes with a set of strict regulations that must be followed. It would be intriguing to learn about the history of bonded warehouses and how their use has evolved over time.
Specific goods, such as those related to defense, pharmaceuticals, or endangered species, require special import or export licenses. These licenses can lead to significant processing delays, making understanding their requirements especially important for shippers working with sensitive products. The question arises about how governments decide what products require licenses and if this system is truly efficient in deterring illegal activities.
Furthermore, duty drawback programs exist in several countries, allowing companies to recover a portion of duties paid on goods that are returned or not utilized. To receive these refunds, businesses must meticulously maintain detailed records and documentation about the shipments. It would be interesting to understand how this program's effectiveness is evaluated and whether the administrative overhead is worth the potential refunds.
The increasing prevalence of e-commerce has altered international customs processes. Simplified clearance procedures are now offered for smaller packages. This shift brings its own unique challenges for compliance, as duties are often handled upfront by these platforms, modifying how businesses manage their international shipping logistics. It seems like we are still at the very beginning of understanding how e-commerce is redefining the global logistics landscape.
Ultimately, the correct preparation of shipping documentation is vital. Missing or inaccurate documents can lead to substantial delays, penalties, and even confiscation of goods. It would be beneficial to understand the penalties a company faces in different countries and whether they are proportional to the error involved.
Customs practices also vary significantly from country to country due to both legal and cultural factors. Some emphasize rapid processing, while others prioritize in-depth scrutiny. These differences suggest that companies need to adapt their shipping processes based on their destination, which can be a challenging undertaking given the global scale of international trade.
In summary, international customs processes are not easily standardized. Each country's unique legal and cultural norms are intertwined with these customs processes, which has made them difficult to simplify and standardize. It seems likely that new methods for international logistics are still emerging as the world becomes increasingly interconnected through trade and e-commerce.
7 Essential Components of Sample Shipping Policies That Reduce RFP Processing Time - Order Processing Cutoff Times For Same Day Dispatch
When it comes to same-day delivery, order processing cutoff times are essential for managing expectations and ensuring shipments go out on schedule. Companies often set these times between the afternoon and early evening, usually between 2 PM and 5 PM, to ensure they can process and ship orders before the end of the business day. These times are influenced by factors such as how much a company can handle in a given day, along with the networks they use for getting things to customers. For customers who need something urgently, knowing the order processing cutoff helps them make informed decisions and plan accordingly. It's also crucial that businesses clearly communicate these cutoff times, especially around peak shopping times like the holidays or during public holidays when schedules might be different. This clear communication is a key part of keeping customers happy and making sure their orders are handled correctly. As customers come to expect faster and faster shipping, businesses need to make sure their order processing methods keep up, or they risk falling behind in a market that's increasingly focused on immediate gratification.
1. **The Cutoff Conundrum:** The point at which orders are no longer considered for same-day shipping, typically set between 2 PM and 4 PM local time, is a crucial element in order fulfillment. However, finding the sweet spot for this cutoff time can be tricky, often depending on carrier schedules and internal operations. It's a balancing act between meeting customer expectations and managing logistical capacity.
2. **Happy Customers, Clear Cutoffs:** Research suggests that being transparent about order cutoff times has a positive impact on customer satisfaction. Providing clear information about when orders need to be placed for same-day delivery helps set expectations and build trust, which can foster customer loyalty.
3. **Automation's Potential:** Implementing automated systems to manage cutoff times can potentially boost order processing efficiency by as much as 30%. This suggests that replacing manual processes with technology can streamline the whole process, but it also begs the question: how easily can these automated systems adapt to changes in carrier schedules or internal workflow fluctuations?
4. **Carrier-Specific Differences:** The cutoff time for same-day shipping isn't a one-size-fits-all policy. Different carriers might have their own preferred cutoff times, especially for express services. This variability emphasizes the importance of understanding each carrier's specific requirements to design optimal shipping strategies. It's quite interesting that these services, which are ostensibly designed to be 'faster', have different cutoffs.
5. **Peak Season Adjustments:** During periods of high order volume, such as holiday seasons, companies often need to adjust their cutoff times. They might move the cutoff time earlier to ensure they can meet the increased demand for same-day shipping without disrupting the service. This suggests that logistics strategies need to be dynamic and flexible to address such fluctuations.
6. **Location, Location, Location:** Even within a single country, cutoff times might vary. For instance, a business operating in a densely populated urban area might have a later cutoff time than a business in a rural area with less robust logistics infrastructure. This geographical element presents an interesting challenge in creating standardized shipping policies.
7. **Cost of Missed Cutoffs:** If an order misses the cutoff time, it could incur extra fees for the company. These costs can arise from expedited shipping arrangements or carrier penalties, and it's essential for businesses to understand these potential expenses to avoid budget surprises and maintain profitability. It's surprising that missing a cutoff time by only a few hours can lead to a substantial change in price.
8. **When Do Customers Buy?:** Studies show that customers often tend to make purchases later in the day. Businesses with later cutoff times might attract more orders, as they can accommodate this buying behavior. This presents the opportunity to optimize operational schedules to align with the natural flow of consumer orders, but it also could imply longer working hours for fulfillment staff.
9. **Inventory and Cutoff Sync:** To avoid inaccurate cutoff times and overselling, businesses need to integrate their order processing and inventory management systems. This integration ensures that cutoff times reflect real-time inventory availability and avoids the frustration of canceled orders due to stock shortages. It's curious that in an era of real-time data and automated processes, such integrations are still necessary.
10. **International Complications:** When dealing with international shipments, cutoff times become even more complex. Customs regulations, clearance times, and variations in carrier operations in different countries all play a role. Successfully managing these complexities requires businesses to understand the specific nuances of shipping across borders and handle the inevitable bureaucracy that accompanies it. One has to wonder if there's a better, more standardized approach for handling such issues across multiple countries.
More Posts from rfpgenius.pro: