Key Elements of an Effective Maintenance Agreement Contract Template in 2024
Key Elements of an Effective Maintenance Agreement Contract Template in 2024 - Clearly Defined Scope of Work and Services
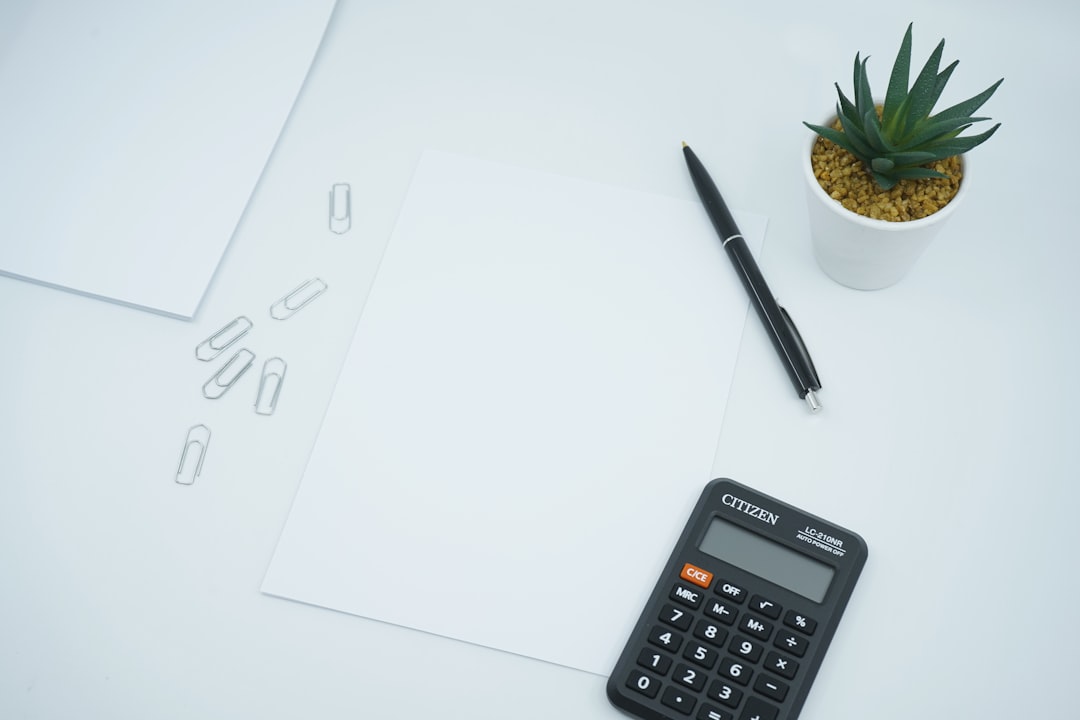
A clearly defined scope of work and services forms the bedrock of any successful maintenance contract. This section acts as a detailed roadmap, spelling out exactly what services are to be provided and who is responsible for what. By being specific about things like how often maintenance is performed, how quickly issues need to be addressed, and what kind of support (whether on-site or remote) is included, the agreement avoids the fuzzy areas that often cause problems down the road.
It's also critical to use straightforward language in this section to ensure everyone is on the same page. This helps build trust between the property owners and the service providers, as both sides understand precisely what they're getting into. A well-defined scope of work not only removes any guesswork about who does what, but it also sets the stage for a productive, long-term relationship based on clear expectations. Without it, you run the risk of misunderstandings and potential disputes further down the line, which nobody wants.
When it comes to maintenance agreements, having a precise and comprehensive scope of work (SOW) is crucial. It acts like a roadmap, detailing every aspect of the services provided and the work to be performed. This specificity can be a game-changer in preventing disagreements and misunderstandings between parties. Imagine the frustration of a facility manager discovering that the agreed-upon "routine maintenance" for a critical piece of equipment doesn't actually include the specific component that frequently fails. A detailed SOW eliminates such grey areas.
Beyond just clarity, a well-defined SOW helps in managing expectations. This includes outlining the type of services to be delivered, the frequency of those services, and the timeframes for completion. It's worth noting that projects with clear, measurable deliverables generally fare better. When individuals and teams understand precisely what constitutes a successful outcome, they're more likely to achieve it. This also extends to cost control. Having clear articulation of tasks allows for more precise budgeting and forecasting, leading to better cost management and potential cost savings over time.
However, a SOW isn't a static document. A crucial element of an effective SOW is its ability to adapt to changing circumstances. Maintenance agreements are often long-term and unexpected changes in operational needs or equipment may arise. Integrating a process for reviewing and revising the SOW can address these unforeseen circumstances. This can help reduce the risks associated with modifications and ensure the maintenance services stay relevant and efficient. Ultimately, a robust SOW ensures that everyone involved—contractors, clients, and stakeholders—are on the same page, resulting in smooth operations and a greater chance of project success. It is a critical building block for fostering trust and efficiency in any maintenance contract, in a manner that may seem overly detailed but which, in reality, streamlines the overall operation and reduces the potential for confusion.
Key Elements of an Effective Maintenance Agreement Contract Template in 2024 - Detailed Maintenance Schedule and Frequency
A detailed maintenance schedule, outlining both the tasks and how often they should be performed, is crucial for a well-functioning maintenance agreement. It's more than just a list of jobs; it's a roadmap that clarifies the expected service delivery. For instance, this section should specify whether tasks are daily, weekly, monthly, or follow some other pattern, all based on what the client needs. Having this structured plan allows those involved to better anticipate upcoming maintenance needs, ensure resources are used effectively, and minimize interruptions to operations.
However, a successful maintenance agreement can't simply be a rigid schedule. It also needs to acknowledge the unpredictable nature of things. Therefore, incorporating processes for handling unexpected breakdowns or other issues within this schedule makes it more robust. This helps ensure the agreement can deal with routine tasks as well as the inevitable emergencies that can occur. In essence, having this level of detail in the contract fosters a stronger bond between the people offering the maintenance services and the clients themselves. More importantly, it also helps create a more effective operational environment. It's a simple step, but it can make a substantial difference.
A well-structured maintenance agreement should include a detailed plan that specifies the frequency of various maintenance tasks. This is more than just a list of things to do; it's about recognizing how often specific maintenance actions are needed to keep things running smoothly. Research suggests that regular maintenance can significantly extend the life of equipment, potentially adding years to its lifespan. This finding really highlights the importance of a thoughtfully created maintenance plan.
Interestingly, the frequency of maintenance is directly tied to cost savings. Organizations that proactively manage maintenance often see significant reductions in their overall costs, possibly up to 18% or more, compared to those who simply react to failures. This underscores the idea that a preventative approach is often more economical in the long run.
Furthermore, a robust schedule helps to minimize disruptions by reducing downtime. It's like a conductor leading an orchestra of maintenance activities. With a detailed plan, organizations can proactively anticipate and prevent issues, limiting unexpected shutdowns that can cause production delays or service disruptions. This can lead to significant improvements in operational efficiency.
The incorporation of data analytics into creating these schedules can further refine their effectiveness. By analyzing historical maintenance data, we can learn which parts of systems fail most frequently and then tailor the schedule to focus on those critical areas. This type of predictive maintenance allows for more targeted and efficient resource allocation.
Safety compliance also ties heavily into maintaining a regular schedule. It's not just about preventing costly breakdowns. Many industries face heavy fines or legal challenges if they don't adhere to specific maintenance regulations. So, the frequency and type of maintenance are essential for meeting compliance requirements and protecting the organization from penalties.
Additionally, a well-structured schedule improves the use of specialized labor. When maintenance needs are understood and planned out, we can ensure that skilled workers are used most effectively. This can help reduce overall labor costs while optimizing the output of expert technicians. It's about matching the right skills to the right task at the right time.
It's also worth mentioning that a detailed maintenance schedule is often tied to warranties. Following the guidelines in the schedule is often a prerequisite for a valid warranty claim. Failure to adhere to the schedule can void the warranty, potentially leaving the organization on the hook for substantial repair costs.
Trends in predictive maintenance indicate that many organizations are embracing data analytics to get ahead of problems. By tracking equipment performance and using advanced analytics, they can predict when a machine is likely to need service. This approach is gaining popularity in industries that rely on critical machinery.
However, it's important to recognize that every piece of equipment has different needs. Some critical systems may require frequent preventative checks, while others might only need annual maintenance. Understanding these distinctions is crucial for creating a tailored schedule. It’s similar to recognizing that a race car needs a more rigorous maintenance plan compared to a family sedan.
Furthermore, we should also think about the range of skills needed for the various maintenance tasks. Some repairs require specialized expertise, while others might be handled by less skilled individuals. A well-developed schedule should acknowledge these differences, helping to ensure that the right people are assigned to the right jobs.
In conclusion, a detailed maintenance schedule is an essential part of a successful maintenance agreement. It's not just a box to check off; it's about implementing a proactive approach to equipment care that leads to increased efficiency, cost savings, compliance, and a better understanding of the needs of each asset. It's a system that can evolve as we learn more about a piece of equipment and its environment. There's a growing recognition that this proactive approach is vital for the long-term health of our assets and for the organizations that depend on them.
Key Elements of an Effective Maintenance Agreement Contract Template in 2024 - Specific Performance Metrics and Quality Standards
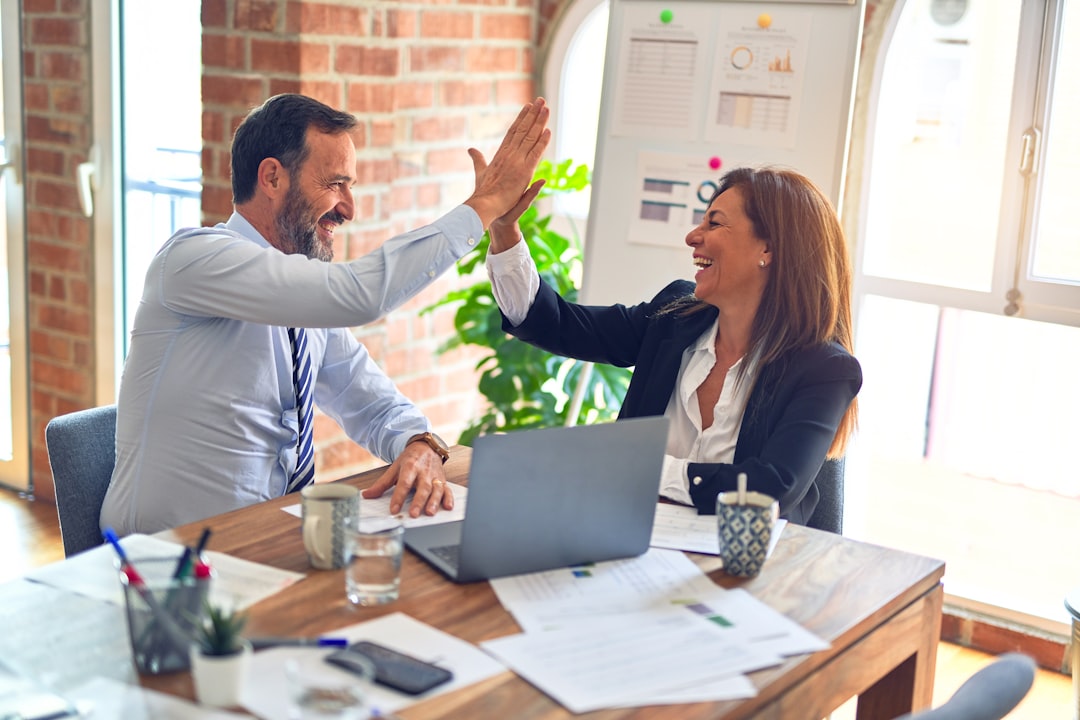
Within the framework of a maintenance agreement, defining specific performance metrics and quality standards is vital for achieving desired outcomes in 2024. These metrics serve as benchmarks to measure the effectiveness of the service provider's work, capturing crucial aspects like how efficiently resources are used (cost), how promptly service requests are addressed (timeliness), how consistently the equipment operates after maintenance (reliability), and the overall quality of the work done. Without a strong focus on measurement, it becomes difficult to assess whether the contract's objectives are being met.
A key component of this focus on standards is the integration of quality assurance processes. These practices help verify that the work performed is up to the standards laid out in the contract. It's important to emphasize that these quality assurance procedures are not just about checking boxes. They are fundamental in establishing accountability and ensuring that the provider's work conforms to specific requirements outlined in the agreement. This part of the contract can include defined inspection protocols and acceptable standards, which contribute to increased transparency and confidence for the client.
Beyond the immediate scope of service, it's also smart to consider the entire process of managing the agreement. In a well-designed contract, the time it takes to finalize and sign the document, as well as the stability of the agreed-upon language over time, can significantly influence the overall success of the maintenance work. Ideally, the signing process should be efficient, with minimal back and forth, and the language of the contract should remain fairly constant to avoid ambiguity and delays later on. It's also worth noting that a contract's effectiveness can be negatively affected by constant modifications and changes to previously established terms.
Ultimately, including specific metrics and standards in the maintenance agreement fosters a transparent and accountable relationship. This transparency allows for better communication and promotes continuous improvement in both the quality of service and the overall management of the agreement. Through the consistent monitoring of these metrics, parties involved can pinpoint areas where processes can be streamlined, outcomes can be improved, and operational efficiency can be further enhanced, solidifying the value of the contract.
Contract performance management aims to get the most out of agreements while minimizing risks and making sure everything's done according to plan. Setting clear, measurable goals for improvements in maintenance agreements helps make things better. We can measure performance using things like cost, how quickly things are done, how reliable equipment is, and the overall quality of the work. This is especially important for contracts where the focus is on results, and it helps to define the exact work to be done along with specific performance metrics.
The time it takes to go through the entire contract process, from starting to finishing, is a crucial metric, too. It's a good idea to keep track of how things are going, looking for ways to improve and be more efficient. When contracts are performance-based, a plan for ensuring quality is needed to check up on the work that's done. A quick turnaround on getting contracts signed and minimal changes to the initial agreements are good signs of effective contract management.
Sometimes contracts have incentives for both sides based on performance, encouraging them to work together towards shared goals. Using a variety of performance metrics can help us understand how efficient, effective, and compliant a maintenance contract is. We can use them to gain insights and manage the process better.
There's a lot of variability in how businesses use standards for asset management. For instance, the ISO 55000 series is a common framework, but not everyone uses it the same way. This makes it hard to compare performance across different organizations. It's interesting to look at how well-kept records can improve performance by up to 25%, hinting that documenting everything helps to find recurring issues and adjust maintenance strategies for the better.
Another thing to consider is that unplanned downtime can be a very expensive issue, with some reports suggesting it can cost manufacturers hundreds of thousands of dollars per hour. This illustrates that performance metrics, as well as quality standards, are very important to keeping operations running smoothly. Root cause analysis is also important; effectively applied it can resolve many equipment problems, suggesting that good quality standards help foster continuous improvements in maintenance. Predictive maintenance has the potential to decrease costs and increase profitability, and is a good example of how tying specific metrics to quality benchmarks can improve overall operations.
We shouldn't ignore the importance of the human element either. When maintenance metrics and quality standards are clear, employees tend to get more engaged and committed to meeting expectations, which can have a positive effect on the entire operation. Regulations are a big driver for maintenance agreements, and meeting these standards is often tied to avoiding fines that can range from thousands to millions of dollars. Interestingly, meeting quality standards can extend the lifespan of equipment significantly, and companies who effectively plan for this are able to plan their operations in a more efficient way.
It’s also important to consider that implementing these types of systems has an upfront cost, but that the investment is usually recovered within just a couple of maintenance cycles through reductions in down time and increases in efficiency. We should think of maintenance as a constantly evolving activity where we gain a deeper understanding of the equipment and learn to optimize how we care for it. This continual improvement helps improve the long-term health of an organization's assets and leads to better outcomes overall.
Key Elements of an Effective Maintenance Agreement Contract Template in 2024 - Comprehensive Pricing Structure and Payment Terms
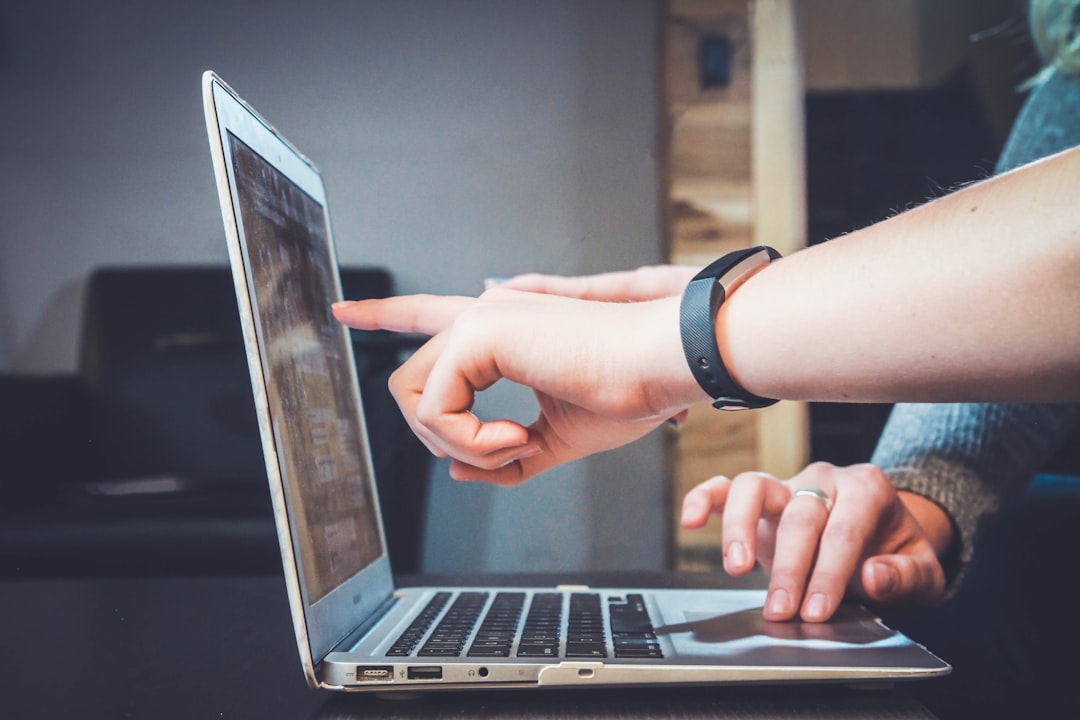
A solid maintenance agreement needs a clear pricing plan and payment schedule. This is crucial for building trust since it removes any confusion about costs and charges. The contract should outline the total expenses, including any regular payments throughout its term. Additionally, the agreement must define when and how payments are made to ensure a smooth financial flow and that both sides fulfill their commitments. In 2024, we're seeing these pricing structures become more flexible, allowing for customized solutions based on each project's financial needs. This approach can also help foster more enduring working relationships. While clear pricing seems simple, it is a crucial part of a well-functioning contract, and getting it wrong can create conflict between the parties. It's important to also think about how any changes in services might impact the cost, and factor that into the pricing structure, and payment schedule. This flexibility in pricing is increasingly important as maintenance contracts often cover long durations, and unforeseen changes in a project's scope of work or other circumstances can arise. While some might think this section is less important than other parts of the contract, it is just as vital, as failure to understand the costs involved can lead to disagreement and conflict.
When thinking about the financial side of a maintenance agreement, things are getting more complex and nuanced. We're seeing a shift towards more flexible pricing arrangements. For instance, some contracts are using "dynamic pricing," where the cost can change based on how much a piece of equipment is used or what's happening in the broader market. While this approach could potentially lead to cost savings, it can also make budget forecasting a bit trickier.
On the payment side, we're seeing greater flexibility, with options like "pay-per-use" or subscription-based models becoming more common. This can be a real help for organizations that want to better manage their cash flow while still making sure their equipment is properly maintained. It's fascinating how these payment structures are evolving.
Another interesting trend is tying payment to performance. There's evidence that contracts which link compensation to how well the maintenance is done lead to better service. Essentially, if the contractor is paid based on how reliably the equipment runs, they're more likely to put in the extra effort to ensure things go smoothly. It's an interesting incentive-based approach.
However, it's important to be aware of the potential downsides to payment delays. Studies suggest that late payments in maintenance agreements can have a negative impact, possibly leading to poorer service and even increased risk of equipment breakdowns. It makes sense, as it can strain the relationship between the client and the maintenance provider. Maintaining timely payments is important to foster a collaborative and productive relationship.
The cost of a maintenance agreement can also vary significantly based on where you are located. Understanding regional factors like labor rates and the price of materials can be helpful in structuring the pricing agreement effectively. This is a bit like a "local cost of living" adjustment for equipment maintenance.
Technology is also playing an increasingly important role. With the integration of sensors and the Internet of Things (IoT) into agreements, we can now monitor equipment performance in real-time. This can then be used to adjust pricing based on how the equipment is actually being used. This is a step towards greater transparency in contracts, a development that deserves further scrutiny.
Of course, there are consequences for not meeting the payment terms outlined in the agreement. Failing to adhere to the payment schedule could lead to penalties or additional costs, which is a strong incentive for being organized. Clarifying and following the payment terms is crucial to maintaining a stable financial situation.
We're even seeing incentives like discounts for early payments in some contracts. This is a smart way to encourage prompt payment and strengthens relationships in the long run, while also providing a cost-saving incentive.
Another trend worth exploring is "life-cycle costing." This involves considering the total cost of owning and maintaining an asset over its entire lifespan. It's a comprehensive approach that can assist organizations in making better decisions regarding their assets.
Finally, we're seeing a general move towards digital payment systems within maintenance contracts. This reduces the administrative burden and speeds up payment processes, streamlining the overall contract management process. It’s a very practical way to reduce overhead, though it raises questions about data security and potential reliance on specific platforms.
While it's still early days for some of these trends, they offer some interesting insights into how the financial aspects of maintenance agreements are changing. It seems that, with the increased use of technology and changing client needs, the contracts themselves are moving towards a more adaptable and performance-focused structure. It's a dynamic space, worthy of continued study and evaluation.
Key Elements of an Effective Maintenance Agreement Contract Template in 2024 - Liability and Insurance Requirements
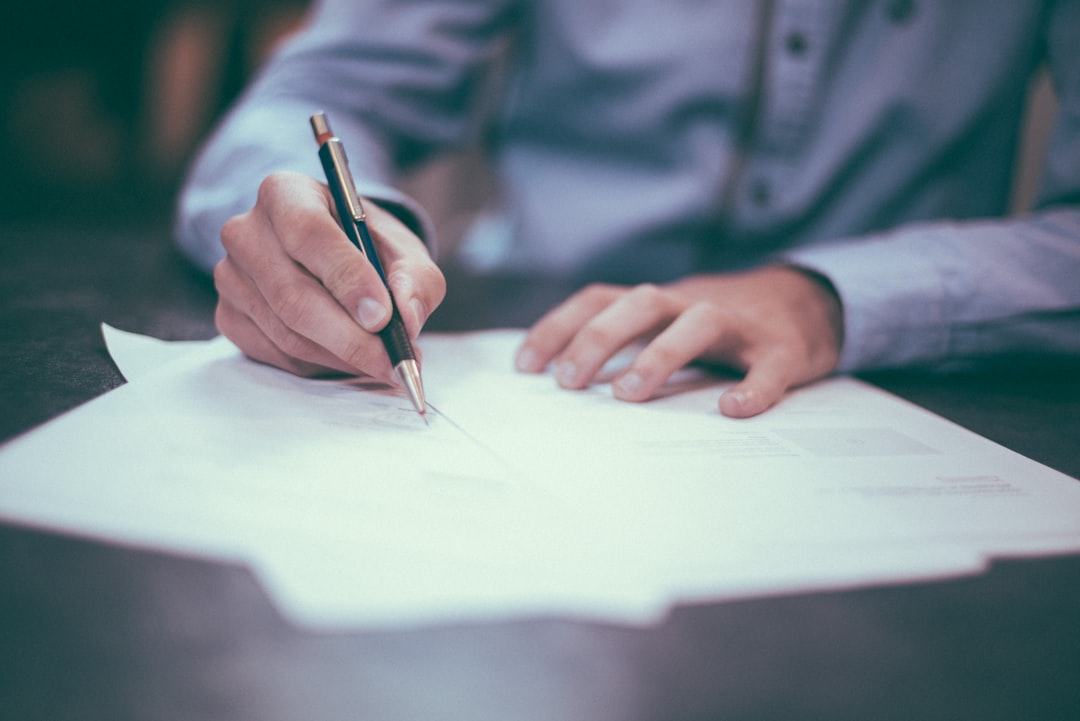
**Liability and Insurance Requirements**
When drafting a maintenance agreement, it's crucial to clearly outline liability and insurance responsibilities. This section acts as a safety net, defining who's responsible for potential damages, injuries, or accidents that could occur during the course of the maintenance work. By being specific about the types and amounts of insurance required, the agreement helps protect both the service provider and the client from unexpected financial burdens and legal challenges. This clarity is important because it promotes accountability and establishes a shared understanding of how risk will be managed, which builds a stronger relationship between the parties. If these elements are overlooked, it could lead to significant problems and unforeseen costs, making them a critical element of any comprehensive maintenance contract in 2024. While some might think these provisions are secondary, they are just as crucial as other parts of the contract, since potential issues can disrupt operations and harm relationships.
When crafting a maintenance agreement, it's crucial to think about potential risks and how to handle them. One important part is defining liability and insurance requirements. There are various types of liability insurance, such as general liability, professional liability, and completed operations insurance, each designed to cover specific situations. For instance, general liability might cover accidental injuries on a site, while professional liability addresses potential errors in the maintenance service itself. Which types are best depend on the specific work being done, and understanding this is critical when writing a contract.
Also, it's worth noting that many places now require specific minimum levels of liability coverage. This is usually to protect third parties from harm, and failing to meet these requirements can lead to significant penalties, like fines or even the suspension of business operations. So, ensuring compliance with local laws is a must.
However, you need to pay close attention to the fine print when looking at insurance policies. Most policies have limitations, often excluding things like intentional damage or losses caused by specific disasters. If an unforeseen issue arises, and it's not covered by the policy due to one of these exclusions, it could create a major financial burden for the client or the service provider.
Insurance costs can also be linked to a company's safety record. Companies with a good history of adhering to safety protocols and having few claims might get better rates. It's something to think about as part of your operational strategy. It highlights the value of having a culture of safety within an organization.
Furthermore, when negotiating the contract, you'll likely discuss the deductible amount for the liability policy. Higher deductibles can lead to lower premiums, but they also mean the client or the service provider will have to pay more out-of-pocket if a claim needs to be filed. This can become a strategic part of negotiation.
Things get even more complicated if you're dealing with multiple companies—a general contractor and its subcontractors. Each entity likely has its own liability insurance policy. If there's a gap in coverage, or if there's confusion about who's covered under what policy, it can create serious problems if an issue arises during the maintenance work. To avoid this, it's critical to be very precise in the contract about who's responsible for what insurance.
The contractor's past claims history is another element that can impact the cost of insurance. If a company has filed many claims, it may get higher premiums from insurance providers, potentially influencing the service price. It is an interesting and often overlooked aspect of business operations.
Additionally, there's a need to factor in new trends like cyber liability coverage. With the increasing use of technology and remote maintenance, it's more important than ever to protect against data breaches and other technological issues. This shows how the insurance landscape is changing.
Moreover, different states can have varying liability and insurance requirements. It's a potential problem for companies that work across multiple states. It's important to be aware of these differences and ensure that the contract complies with all applicable state regulations to avoid costly legal battles.
Finally, an interesting point is that the type and strength of the liability insurance a contractor carries can even be a bargaining chip in a negotiation. A contractor with strong coverage can be seen as lower risk, which might give them an edge in securing a contract.
Essentially, defining liability and insurance requirements is vital for a smooth, problem-free maintenance agreement. It protects everyone involved and helps to minimize potential conflict. It requires diligence and a good understanding of the risks involved in each situation. It's another fascinating detail about how contracts function.
Key Elements of an Effective Maintenance Agreement Contract Template in 2024 - Termination Clauses and Contract Renewal Options

When crafting a maintenance agreement in 2024, it's crucial to include clear and concise language outlining how and when the contract can end, as well as how it might be extended. Termination provisions should detail the circumstances under which either the service provider or the client can end the agreement, including specifics about any breaches of contract or performance expectations. This clarity is essential for protecting both parties' interests and preventing potential disagreements later on.
Renewal clauses play a significant role in ensuring smooth transitions. These sections should be straightforward and easy to understand so both sides are on the same page regarding how the contract can be continued. Ambiguous or poorly-written renewal clauses can lead to conflicts about the terms of the new agreement. Ideally, the contract should clearly specify any required actions or notice periods to initiate a renewal.
Beyond the initial drafting, ongoing review is essential for effective contract management. It's good practice for both parties to revisit the contract before the renewal date to ensure the terms and obligations still align with current needs and expectations. This type of review helps prevent the situation where a contract continues, despite changes in operational requirements or technological advances that might make the original terms obsolete or disadvantageous for one of the parties. Additionally, regular review can identify opportunities to improve the agreement and optimize services over time.
Another important best practice is to include ample time for notice before a contract expires. This allows for efficient planning and adjustments to ensure a seamless transition into a new contract term or a complete ending of the service relationship. Six months' notice is a common industry standard, but it's best to tailor this to the specific needs of the agreement.
In short, carefully written termination and renewal options within the maintenance agreement create a transparent and responsible relationship between the parties. The goal of these provisions is to ensure a degree of predictability, promote clarity, and foster a collaborative approach to maintenance service agreements. However, without vigilant review and consideration of changes, even the most carefully crafted clauses can become irrelevant, so constant reevaluation is advisable.
When it comes to maintenance agreements, the parts about ending the contract (termination) and how to extend it (renewal) are often where problems arise. It's like a hidden minefield of potential confusion if these sections aren't crystal clear. Research indicates that well-defined termination clauses can lead to better contract adherence, helping to avoid misunderstandings that can lead to disputes.
With the growth of automated systems, we're starting to see more automated contract renewal clauses pop up. While this can certainly make things easier operationally, it also creates a new risk: If you don't keep a watchful eye on your agreements, it's possible to get stuck in a contract with unfavorable terms. You need to stay on top of it to make sure it's still the best fit for your needs.
Termination fees are another intriguing part of the mix. They can be a safety net for service providers, offering some financial assurance if the contract is ended early. But if these fees are too high, they can deter clients from using the service in the first place, or make them reluctant to end a contract even when service quality is poor. There seems to be a balance to be found here.
Some newer contracts are incorporating what's called a "snapshot" clause, which essentially gives you a performance review checkpoint before the renewal period. It's like a scientific experiment to see how the service is performing over the course of the contract. This approach offers clients a chance to make a more informed decision about whether to continue or end the agreement based on their direct experience with the services.
Contracts are evolving, and we see a shift towards more flexibility in renewal options. For instance, agreements may include various lengths of time and different conditions based on the performance of the provider. Clients appear to prefer these more adaptive contracts because they allow them to respond to changing needs. This type of flexibility also helps to keep the provider motivated to deliver consistently good service.
A staggering 50% of contracts require unnecessary revisions due to unclear legal language in these termination and renewal sections. That really underscores the importance of working with legal experts to review contract templates and to draft contracts as clearly as possible. This careful attention to legal detail is essential to protect your interests.
On the flip side, termination clauses can give you a negotiating advantage. If you have a solid ability to terminate a contract for subpar performance, it can give you a bit of power during the initial contract discussions. Service providers understand that they're more likely to be held accountable if the contract is easy to terminate.
Ending a contract can also affect other parts of your operations. If you terminate a maintenance contract, it can have a ripple effect on related service contracts. This makes the importance of things like the notice period and any transitional arrangements clear – a detail that often gets overlooked.
The legal requirements around termination and renewal can also vary depending on where you're located. If you're operating in multiple regions, contracts need to address these local regulations or you risk running into legal issues.
Lastly, as data analytics become more prominent, contracts are incorporating clauses that allow for performance reviews using real-time data. By building in a clause that allows for termination based on performance metrics derived from these systems, there's a clear incentive to provide high-quality maintenance services, and this creates better accountability for providers.
Overall, these termination and renewal clauses are often overlooked but crucial parts of any maintenance contract. Taking the time to craft these sections carefully and to understand their implications can save a great deal of hassle later on. It's all about reducing the risks and maximizing the effectiveness of a contract that is often central to smooth operations.
More Posts from rfpgenius.pro: