Key Elements of an Effective Maintenance Contract Agreement in 2024
Key Elements of an Effective Maintenance Contract Agreement in 2024 - Scope of Services and Responsibilities Defined
Within a maintenance contract, defining the "Scope of Services and Responsibilities" is absolutely critical. This section outlines exactly what the service provider is expected to do, covering things like how often they'll perform maintenance, how quickly they'll respond to issues, and what kind of support they'll offer (on-site or remotely). Using clear and simple language when describing these obligations is key. It helps ensure both sides are on the same page, preventing misunderstandings and disagreements later on.
A well-defined scope doesn't just help manage costs; it also contributes to smoother operations. Property owners and facility managers gain the ability to better plan their maintenance schedules and ensure equipment operates reliably. In essence, having a precise scope makes managing maintenance easier and more consistent. This translates to better overall maintenance outcomes and greater operational stability.
Defining the exact range of services and who's responsible for what is crucial for a successful maintenance agreement. This clarity prevents misunderstandings about who does what, reducing the chance of arguments and promoting a smoother working relationship between the property owner or manager and the service provider.
When a contract lays out everyone's duties clearly, it generally leads to fewer delays in getting maintenance done. Knowing who is responsible motivates them to carry out tasks promptly.
We can measure how well the maintenance is done by defining key performance indicators (KPIs) tied to specific services within the scope of work. This gives a way to check performance, which is really important for keeping the quality of service up over time.
If a contract doesn't specify responsibilities carefully, you can end up with what's known as "scope creep." This is where extra tasks get added without being officially agreed upon, which can blow budgets and make projects take much longer.
Some maintenance contracts might also spell out technology requirements that have to follow the manufacturer's guidelines. This can be helpful for keeping warranties valid and extending the life of equipment.
It's very common for maintenance contracts to include response times for emergencies. How quickly the service provider responds in these situations is critical for keeping systems running and businesses going without interruptions.
Another aspect to think about is safety. Including specific safety requirements in the scope of services might reduce accidents. Making safety a key part of the maintenance plan is a worthwhile goal.
A clear division of duties can also help with efficiently using resources. Maintenance teams can work more effectively if they know exactly what they are responsible for, and this can also minimize downtime.
Contracts that have a pre-defined system for escalating unresolved issues tend to see faster solutions. This protects the smooth running of operations and reduces risk.
Finally, setting up clear communication methods within the scope can improve transparency and collaboration for everyone involved. This is essential to make maintenance work as well as it possibly can.
Key Elements of an Effective Maintenance Contract Agreement in 2024 - Smart Maintenance Approaches and Technology Integration
Within the landscape of 2024 maintenance contracts, incorporating "smart" approaches and the integration of advanced technologies is no longer optional but essential. Smart maintenance, in essence, utilizes digital tools and data analysis to make maintenance more efficient. Think of it as a shift towards more proactive, data-driven decision-making in the maintenance world.
This trend necessitates a more organized approach to implementing smart maintenance, which could involve benchmarking against current practices, establishing clear objectives, and prioritizing crucial initiatives. Successful smart maintenance depends heavily on how well an organization can integrate these technologies both internally (within its own operations) and externally (with partners and suppliers). This integration is vital for crafting maintenance plans that effectively tackle the unique challenges of specific operations.
The field of maintenance management is now increasingly focused on validating claims about the effectiveness of these smart technologies with real-world evidence. In other words, the industry is moving away from speculation and toward demonstrating the actual impact of these technological innovations. This push for greater evidence-based practices indicates a significant maturation of maintenance strategies as we move into the future.
How maintenance is handled is changing a lot with new technology. One area getting attention is using digital tools to manage maintenance, especially in factories. This approach, often called "Smart Maintenance," focuses on designing organizations to use digital tech to keep things running smoothly. It emphasizes using data to make better decisions and involves both people within the organization and outside partners.
A key aspect of smart maintenance involves understanding how to use technology to predict problems. For example, using algorithms and historical data can help predict when equipment might fail, allowing us to plan for maintenance before it becomes a major disruption. This, in turn, can reduce the time equipment is out of service and associated costs.
The Internet of Things (IoT) is another core element of Smart Maintenance. By connecting sensors and devices, we can gather information in real-time, giving us immediate insight into potential issues and allowing for quicker action. Another related concept, using "digital twins"—virtual replicas of physical machines—has a lot of potential for planning maintenance in advance. By simulating how components might react under different circumstances, we can optimize maintenance schedules and potentially prevent failures.
Artificial intelligence (AI) has been helpful in diagnosing maintenance problems. Machine learning algorithms, in particular, can process information about past failures and guide technicians to the root cause of a problem faster and more accurately. Augmented reality (AR), a technology that overlays digital information on top of physical equipment, has begun to be used to help with repairs. By providing step-by-step guidance to technicians, it has shown the potential to reduce repair times significantly.
We're also seeing the use of mobile devices in maintenance. Technicians on site can access important information instantly, submit work orders, and get updates, all of which speeds up the whole process and makes communication easier. A shift towards condition-based maintenance is also happening, where the focus is on when machines need maintenance based on their condition instead of a set schedule. This strategy can potentially cut maintenance costs and extend the lifetime of equipment. Data-driven decision-making is becoming more common as a result of this. By integrating data and analytics, organizations can make choices based on reliable information, leading to better efficiency and smarter use of resources.
Remote monitoring technology, thanks to advanced sensors, lets us keep an eye on systems from afar. This means we can spot issues before they escalate, leading to less travel time and operational disruption. While the use of technology is generally helpful for improving maintenance, there are hurdles. One of these is the lack of standardized protocols across the various systems and technologies. Without standards, we risk incompatibility problems which can make using these technologies more complex and limit their usefulness. This area requires attention so the potential of smart maintenance can be fully realized.
Key Elements of an Effective Maintenance Contract Agreement in 2024 - Fee Structure and Cost Management Strategies
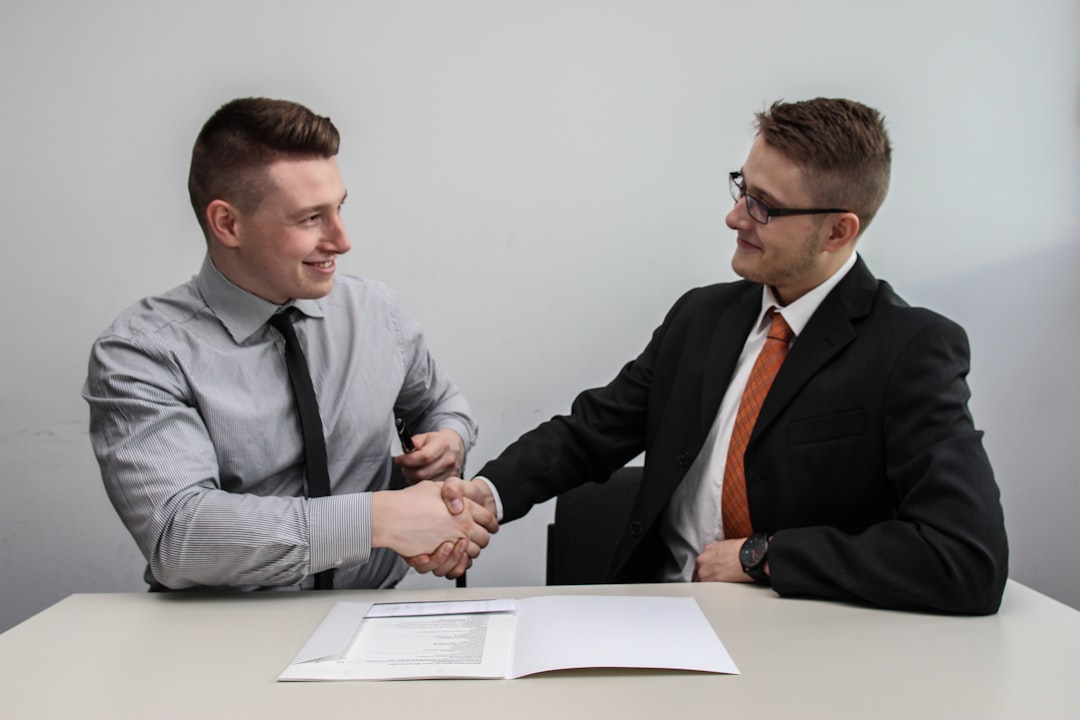
In the context of 2024 maintenance agreements, a transparent and well-defined fee structure is crucial. This means outlining all costs, including any recurring payments, upfront to avoid confusion and potential disputes. Open communication about financial aspects helps build trust between property owners or managers and service providers.
There's a growing trend toward longer-term contracts for maintenance, primarily due to the potential for reduced overall costs. These contracts can also provide a greater degree of stability for maintenance operations, which can be beneficial in planning and scheduling.
It's vital to ensure the contract's cost structure reflects the goals and objectives of the facility. This involves carefully evaluating different pricing models to ensure the agreement provides the best value for the facility's needs. Matching the contract's finances with the facility's aims can improve efficiency and prevent unexpected costs.
Beyond the specific contract terms, fostering a shared understanding of fee structures and cost management across all stakeholders is essential. Training and communication are necessary to ensure all parties are aware of how costs are determined and how they can contribute to keeping costs under control. This level of awareness promotes a sense of shared responsibility for the success of the contract and results in better maintenance outcomes.
The way maintenance contracts are priced can be quite varied. You see things like fixed prices, where you pay a set amount regardless of how much work is done, or cost-plus, where the provider gets reimbursed for expenses plus a markup. Then there's time-and-materials, where you're billed based on how long the work takes and the parts used. It's important to think about which of these makes sense for the specific maintenance needs and the budget you have.
One thing that can really mess up a maintenance budget is "scope creep," where things get added on later without being formally agreed upon. It's been noticed that these kinds of unplanned changes can bump up the cost by a significant amount, as much as 25% to 50% of the initial estimate. This really highlights the importance of laying out all the expected work and responsibilities clearly upfront.
While using newer technologies can often make maintenance more efficient, there are usually some upfront costs associated with getting them implemented. Sometimes these costs can be a sizable chunk of the overall maintenance budget, somewhere between 10% and 30%. So, it's important to carefully weigh the immediate expense against the potential future savings when thinking about using these technologies.
It's been found that if you take a proactive approach to maintenance, like scheduling preventive maintenance tasks, you can usually save around 12% to 18% of the annual maintenance costs. Not only does that help with cost, but it can also increase how long equipment lasts and reduce unexpected breakdowns.
Maintenance contract agreements really need good documentation. If things are poorly written or not kept organized, it can lead to more disputes and disagreements, potentially adding 20% or more to the cost of doing the maintenance. It just reinforces the need for good record-keeping and a clear contract.
The price of labor can differ depending on where you are, what kind of work is being done, and how skilled the technicians are. The hourly rate for skilled technicians can range from a low of $50 to over $150 depending on location and expertise, for instance. That variability means budgeting and negotiating have to be done carefully when creating a contract.
Ignoring industry regulations in a maintenance contract can lead to serious penalties. It could mean thousands or even millions of dollars in fines. So, it's important to make sure the contract includes compliance checks and follows all applicable rules and regulations.
If you use predictive analytics to figure out when things might need maintenance, it's been reported that companies have seen a 20% return on investment. This is mostly because downtime and overall costs go down. That's something to consider if you're trying to maximize the effectiveness of your maintenance strategy.
Some maintenance agreements split the risk between the parties. This means costs are linked to how well things are maintained according to certain targets. These types of arrangements might push service providers to do a better job, but it can make forecasting harder and require careful tracking of performance.
By studying how much other companies in a similar industry spend on maintenance, you might find your costs are higher than they need to be. Some studies suggest that if you align your maintenance spending with industry averages, you could cut costs by as much as 15%. Analyzing those benchmarks can be a good way to spot areas where spending can be streamlined without sacrificing the quality of maintenance.
Key Elements of an Effective Maintenance Contract Agreement in 2024 - Compliance Testing and Performance Metrics
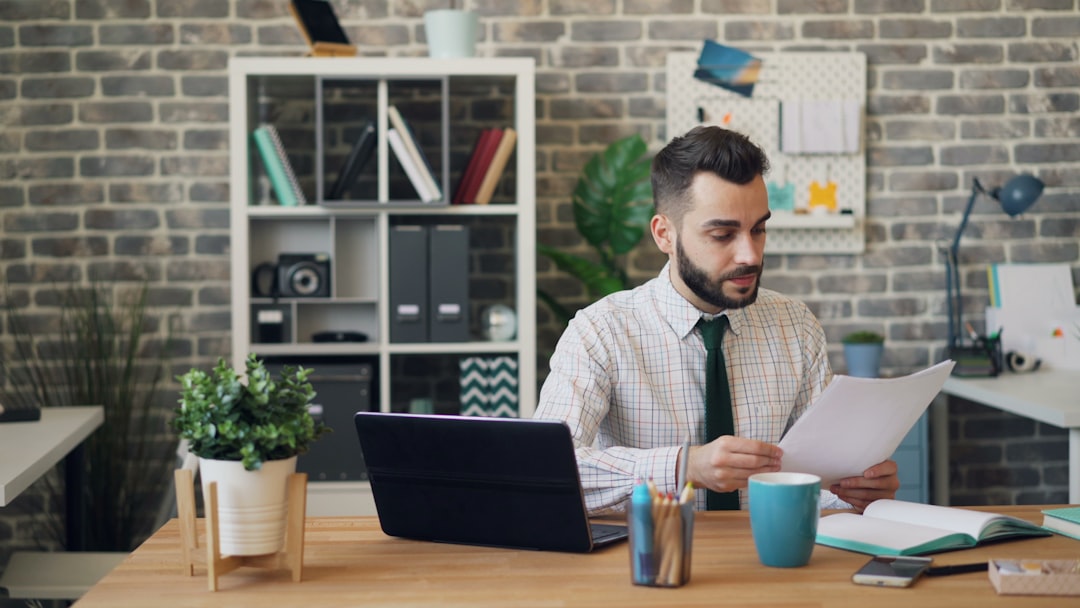
In today's maintenance contracts, evaluating compliance and performance through testing and metrics is becoming more important. Defining clear performance benchmarks, using Key Performance Indicators (KPIs), enables organizations to verify if they're following both their internal policies and any relevant external regulations. This helps ensure the quality of maintenance services remains high throughout the contract's duration.
It's crucial to regularly monitor these compliance metrics. The information gathered provides valuable insights, enabling data-driven decision-making and adjustments to contract strategies. This dynamic approach enhances overall contract success and performance.
Furthermore, a well-structured contract monitoring plan is a must for tracking both compliance and performance from beginning to end. It helps everyone involved understand how well the maintenance is being done and highlights any areas that need improvement. This emphasis on monitoring strengthens accountability and ensures everyone is aware of their responsibilities in the maintenance agreement.
The adoption of smart maintenance technologies in recent years is also changing the approach to compliance and performance. Data sharing becomes increasingly vital, as does fostering seamless collaboration between the property owner/manager and the service provider to manage the maintenance effectively. The integration of real-time data into the monitoring process is essential in this new environment.
Compliance testing and the metrics used to measure performance within maintenance contracts are crucial aspects that can vary significantly across different industries. For example, healthcare facilities, due to the direct connection to patient safety and stricter regulations, tend to have more stringent compliance checks compared to, say, a manufacturing plant. It's interesting to consider how the nature of the operation can influence the level of detail needed for compliance.
It's not enough to just go through the motions of compliance testing; using performance metrics to really assess things can unearth areas where operations could be made more efficient. Research suggests that by strictly following compliance protocols, we can potentially reduce operational costs by as much as 30%. That's a pretty compelling reason to take compliance seriously.
It's alarming to learn that a substantial portion of maintenance contracts—estimates are around 60%—don't meet compliance standards. This often stems from contracts with unclear language and poorly defined performance metrics. It truly highlights the need to be precise and clear in the contractual language to avoid the headaches of hefty penalties later on.
Benchmarks used to assess the service providers in the context of compliance can also differ drastically depending on the context. Organizations using data analytics, for instance, often see a 25% improvement in service quality when compared to those using more traditional methods that don't rely on data. This implies that adopting modern analytical tools can lead to demonstrably better results.
Implementing regular compliance audits can act as a valuable tool both for correcting existing issues and preventing future ones. Studies suggest that organizations who do audits twice a year see around 40% fewer compliance violations than those that skip them. It shows that proactive monitoring can be quite effective.
It's quite surprising to discover that a majority of organizations—upwards of 70%—don't track compliance-related performance metrics consistently. This disconnect between how well they think things are going and the actual results poses a significant risk for maintaining accountability and ensuring that budgets are aligned with performance. This kind of oversight could lead to difficulties in effectively managing resources.
The relationship between how often you do compliance checks and operational downtime is quite striking. Companies that do monthly compliance checks report experiencing a 50% drop in unplanned outages when compared to companies that do them less often. This suggests that even seemingly small changes in the frequency of inspections can have a meaningful impact on operations.
Integrating technology into the compliance process can make the results more reliable. Smart systems capable of real-time analysis of performance metrics can reduce the likelihood of errors made by humans during evaluation by as much as 80%. This enhanced accuracy can lead to more dependable compliance audits.
Failing to comply with regulations can be incredibly costly. Industries can face fines exceeding 5% of their yearly revenue for failing to meet standards. This stark reminder highlights why having a robust compliance testing system within maintenance contracts is absolutely essential.
One unexpected positive outcome associated with robust compliance testing and performance measurement is a potential decrease in employee turnover. Organizations where there's a strong culture of compliance and accountability see about a 15% improvement in job satisfaction. This interesting correlation suggests that employees feel more positive about their work environment when they perceive it as well-managed and transparent.
Key Elements of an Effective Maintenance Contract Agreement in 2024 - Scheduling and Frequency of Maintenance Activities
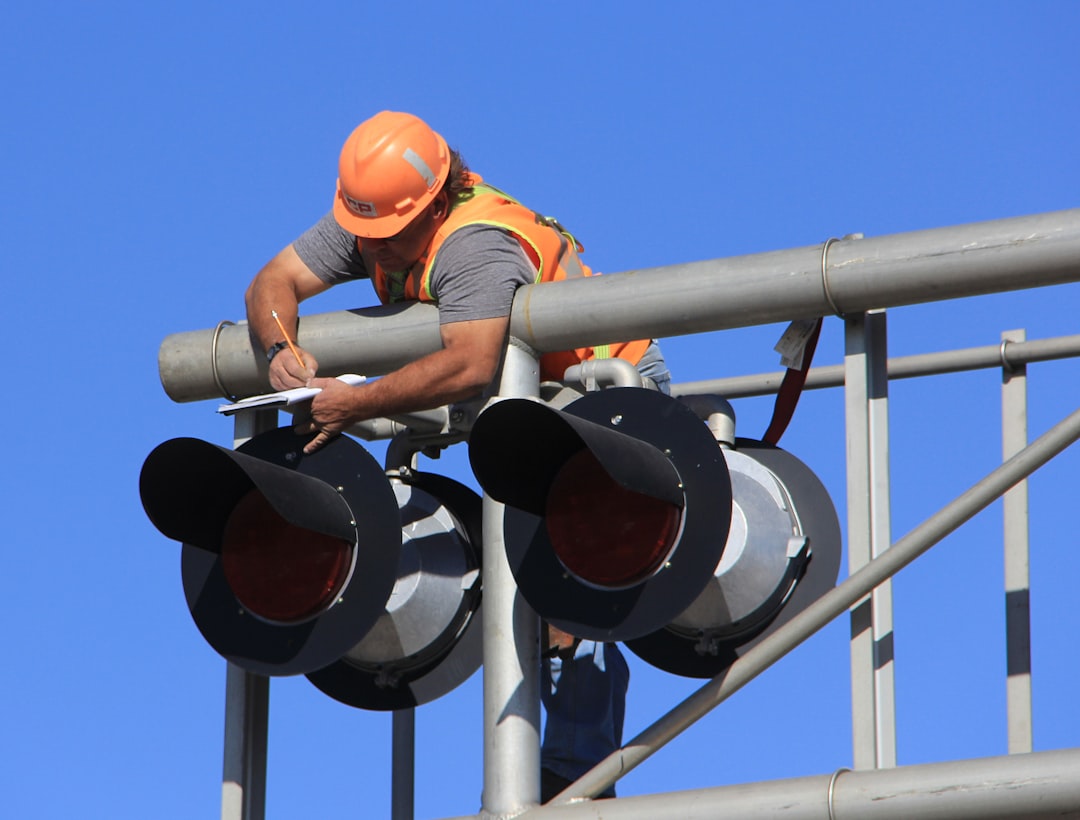
In today's environment, maintenance contracts need to be very specific about how often certain tasks should be done and when they'll happen. This is crucial for keeping equipment working reliably and preventing unexpected downtime. A good maintenance schedule isn't just a list of what needs to be done, it also has to say exactly when it should be done and who is responsible, making technicians accountable for their work. If maintenance activities are planned using data, it allows businesses to prioritize things based on how urgent they are and the state of the equipment, ultimately improving how smoothly things operate. Clearly defining the schedule in the contract is also important for avoiding what's called "scope creep" and preventing delays that can ruin maintenance plans and increase costs. As technology improves, using smart maintenance methods can make scheduling more accurate because they allow for using real-time data to do maintenance before problems arise.
When crafting a maintenance contract, a crucial aspect is defining how often and when maintenance activities should occur. Research suggests that simply having a schedule isn't enough; a truly effective one uses data to understand wear and tear patterns, potentially decreasing equipment failures by over 30%. This finding pushes us to rethink the traditional approach of using arbitrary timelines.
We've also learned that the frequency of specific maintenance tasks can significantly impact how long equipment lasts. Surprisingly, more frequent maintenance can, in some cases, extend equipment lifespan by up to 50%. This contradicts the common belief that less frequent maintenance is cheaper in the long run.
Further complicating matters, some equipment functions better when maintenance is aligned with seasonal usage peaks and dips. Facilities that align maintenance schedules with these patterns experience a decrease in downtime by as much as 25%. This highlights how crucial it is to tailor the schedule to the specific equipment and its operating environment.
The rise of predictive maintenance technologies is altering how we approach maintenance scheduling. Businesses are already seeing improvements in maintenance efficiency, with some reporting gains of up to 20% by using these techniques. These predictive approaches prioritize maintenance based on analysis instead of a fixed calendar, leading to a smarter, more adaptive maintenance strategy.
However, just having a great schedule isn't a guarantee of success. Studies reveal that training maintenance teams on the importance and specifics of scheduled tasks leads to a 40% increase in their adherence to the plan. It's clear that proper training and understanding are as essential as the schedule itself.
Digital tools are playing an increasingly significant role. Organizations that use digital maintenance management software report a 15% decrease in time spent creating maintenance schedules. This shift frees up maintenance teams to focus on performing the tasks rather than just planning them.
Another interesting development is the use of condition monitoring. Real-time monitoring systems that analyze equipment health can help optimize maintenance by adjusting the frequency of tasks based on actual need. This results in a decrease in unnecessary maintenance, potentially reducing it by 30%.
Condition-based maintenance (CBM) has shown tremendous promise in reducing failures. Facilities using CBM have seen a drop in unexpected equipment failures ranging from 25% to 50% compared to those relying on traditional fixed schedules. This demonstrates the power of basing maintenance decisions on real-time equipment condition rather than pre-set intervals.
Integrating risk assessments into the scheduling process further enhances the strategy. By understanding which equipment and operations are most critical, maintenance activities can be prioritized more effectively. This strategy reduces the likelihood of failure by up to 35%.
Interestingly, involving both the service provider and the facility team in the scheduling process has been proven to improve compliance and timelines. Collaborative scheduling improves outcomes by 20%, as it creates a sense of ownership and accountability.
Ultimately, the scheduling and frequency of maintenance activities are complex issues with many factors to consider. A well-defined, adaptive, and data-driven approach can significantly improve equipment reliability, reduce downtime, and ultimately enhance operational efficiency. It's an evolving field that is increasingly relying on data and technology to drive the most effective results.
Key Elements of an Effective Maintenance Contract Agreement in 2024 - Contract Duration and Renewal Terms
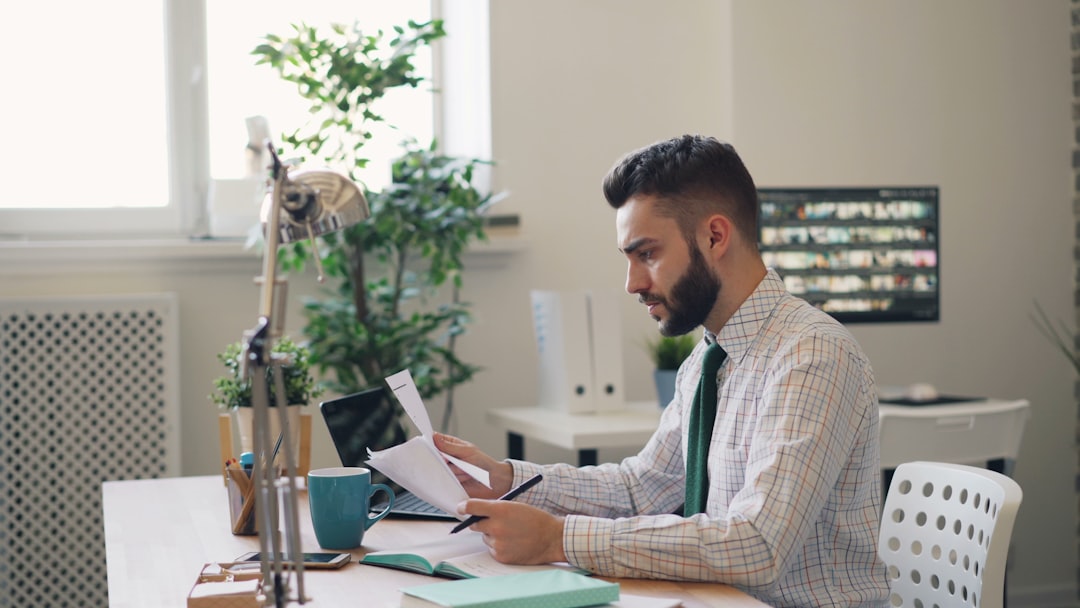
When crafting maintenance contracts in 2024, defining the "Contract Duration and Renewal Terms" is critical for a successful, long-lasting agreement. The way renewal terms are written is important. Clear language prevents confusion and helps avoid problems that could arise if a contract automatically renews or if terms change. There's a growing trend towards longer-term contracts, but it's crucial to review existing contracts before they automatically renew. This is to make sure that the obligations laid out in the original contract are still what's needed and are still relevant. Also, being aware of contract timelines gives a better opportunity to renegotiate terms to help the contract perform as it should. A carefully defined renewal process can go a long way in making sure that operations are stable and consistent. It's a matter of understanding the details in the renewal sections to get the best outcome. While the initial agreement is important, how the contract progresses and gets renewed is equally vital.
When it comes to maintenance contracts, the duration of the initial agreement and the specifics of any renewal process are incredibly important, almost as important as defining the work itself. Renewal terms are basically the rules for extending the contract beyond its original timeframe. If these terms are unclear or ambiguous, it can create a lot of confusion, especially when it comes to understanding exactly how long the contract will last and what happens when it's time to renew. It's a common practice to have a clause that allows the contract to renew automatically, often referred to as an "evergreen" clause. These types of clauses, if not handled correctly, can lead to situations where a service continues even if no one wants it.
One thing I've found fascinating in my research is that automatically renewing contracts, while seemingly convenient, can cause problems. It's easy to miss the renewal deadline, which can lead to keeping a service you no longer need. The length of a contract itself can impact a business's flexibility. Longer contracts can seem appealing because they give you a sense of stability and hopefully predictable costs. However, long-term contracts make it harder to adapt if business conditions change, or if a better service provider appears on the scene. You might be stuck with something that's no longer the best fit for your operation.
It's interesting to consider that proactively discussing renewal terms can give an organization some leverage when negotiating. If you start the conversation early, you might be able to secure better pricing. Unfortunately, it seems that disputes related to contracts crop up quite frequently during the renewal process. A lot of this stems from unclear language. Terms and conditions that were initially OK might no longer align with what's needed. This underscores the need for reviewing and potentially updating those agreements. The frequency of renewals can also impact how well a contract performs. Annual renewal contracts tend to perform better than those with longer terms because the constant check-in helps ensure the service provider is meeting expectations.
There's this whole area of benchmarking that's often overlooked in contracts. Most organizations don't have a good handle on what's considered normal or average for contract renewal terms in their industry. This lack of knowledge means many are probably paying more than they need to when it comes to renewal fees. It's also quite interesting that the initial contract term seems to create a kind of mental commitment. Businesses might become less aware of any issues or inefficiencies once they've signed on to a long-term deal, even if they start to regret their decision.
One of the unexpected downsides of longer contracts is that they can slow down the adoption of newer technologies. This makes sense, though; why would a service provider want to embrace new ways of doing things if they're locked into a long-term arrangement? It's similar to the negotiation window related to seasonal operations; negotiating during slow periods can give a facility more power when trying to get better pricing. If the renewal clause ties service levels to performance, it motivates the service provider to do a better job. It's a way to introduce a healthy bit of pressure to keep service quality high.
The findings related to contract durations and renewals can be both helpful and surprising. It really emphasizes the need to think about the specifics of a contract very carefully and not just automatically agree to default settings. While it's important to have some degree of stability, it's also important to build in some flexibility. If you consider these points as you write the initial contract and the renewal terms, you can hopefully avoid a lot of issues later on.
More Posts from rfpgenius.pro: